Matias Muchnik and Karim Pichara founded NotCo to modernize R&D in the food industry. While it might look like a plant-based food company, NotCo is in the data and AI business—and aims to disrupt R&D in many industries that use animal and plant ingredients.
It was March 2015 and Matias Muchnik was bracing for rejection. The vegan mayonnaise entrepreneur and former banking intern entered the office of Karim Pichara, Professor of Computer Science at UC- Chile and an AI researcher at Harvard. Matias needed a co-founder with AI expertise to launch a firm that he hoped could revolutionize plant-based food R&D.
“I thought there was zero chance of convincing Karim to jump on board this thing,” says Matias, who’d never met Karim before. Matias only knew him by reputation; seven friends had studied AI under Karim.
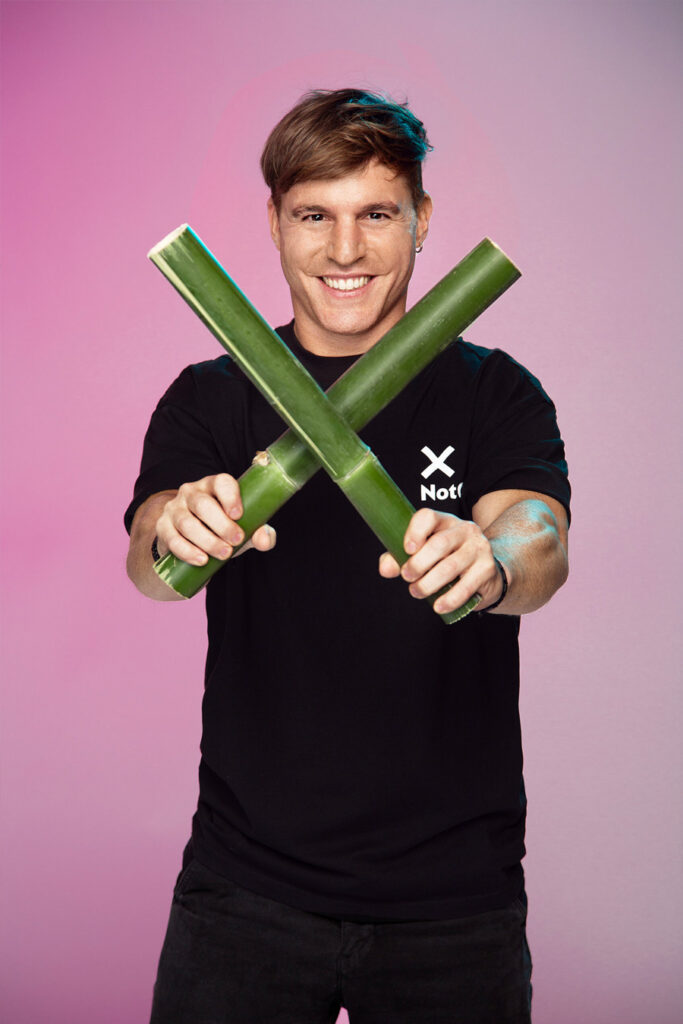
Matias pitched Karim on developing an AI that could propose plant-based formulas that would produce meat and dairy substitutes tasty enough to supplant (no pun intended) the animal-based versions—and thereby reduce their carbon and overall environmental footprints. Matias had a great pitch, but he was also a 20-something with no scientific background.
To Matias’ shock, Karim was impressed. He joined Matias’ fledgling NotCo as a co-founder and CTO. NotCo went on to raise $443 million and reach a reported $1.5 billion valuation, with backing from SOSV, Bezos Expeditions, Tiger Global, and Kaszek Ventures, among others. Just as impressively, Matias and Karim launched animal-based plant and dairy products like NotMilk, NotBurgers, and NotChicken and landed on the shelves of Whole Foods, Sprouts, and Amazon and on the menus at Shake Shack, Starbucks, Dunkin Donuts, and Burger King.
But what did any of that have to do with AI? Far more than those consumer launches might suggest. NotCo developed those products using a proprietary AI that is transforming the speed, cost, and precision of developing plant-based foods. They call the AI “Giuseppe,” and it’s the foundation for their critical partnerships with leading food companies. Products like NotMilk, NotBurgers, and NotChicken are not the end game for NotCo. “We built a Trojan horse, and we’re just starting to release the soldiers,” says Matias.
The middle of three brothers and the son of a banker, Matias was raised on Bloomberg TV and dinner table conversations about finance. The family rebel growing up, he played rugby instead of soccer like his siblings. Rugby turned Matias into a foodie and health nut. He wanted a diet that would improve his performance on the pitch, but nutrition experts never seemed to agree on which foods were “healthy.” Vegan products were particularly confusing. They were the holy grail one day and processed junk food the next.
“Whenever an industry is generating that much confusion, it’s because the industry is broken and there are conflicts of interest,” says Matias, who chose to eat a plant-forward, flexitarian diet.
Matias earned his bachelor’s degree in economics at the University of Chile and landed an internship in banking. Entrepreneurs seemed to be the happiest of his banking clients. That observation, combined with his passion for food, led Matias to launch a vegan mayo startup.
Matias’s venture, Eggless Company, produced, packed, labeled, and shipped vegan mayo from a friend’s garage. It was the right product, explains Matias, because Chileans put mayo on just about everything. Eggless Mayo became the top-selling alt-mayo in the country.
“It’s literally two people in lab coats doing trial and error.”
Matias Muchnik, CEO, NotCo
Matias exited Eggless Company in 2015 and joined an entrepreneurship bootcamp at the University of California-Berkely to figure out his next move in the food world. Matias knew that plant-based products had to capture mass market omnivores to make a difference for the environment.
While plant-based meat and dairy were getting tastier, the glacial pace of food R&D made innovation too slow and prices too high. Food R&D was “archaic,” says Matias. “It’s literally two people in lab coats doing trial and error.”
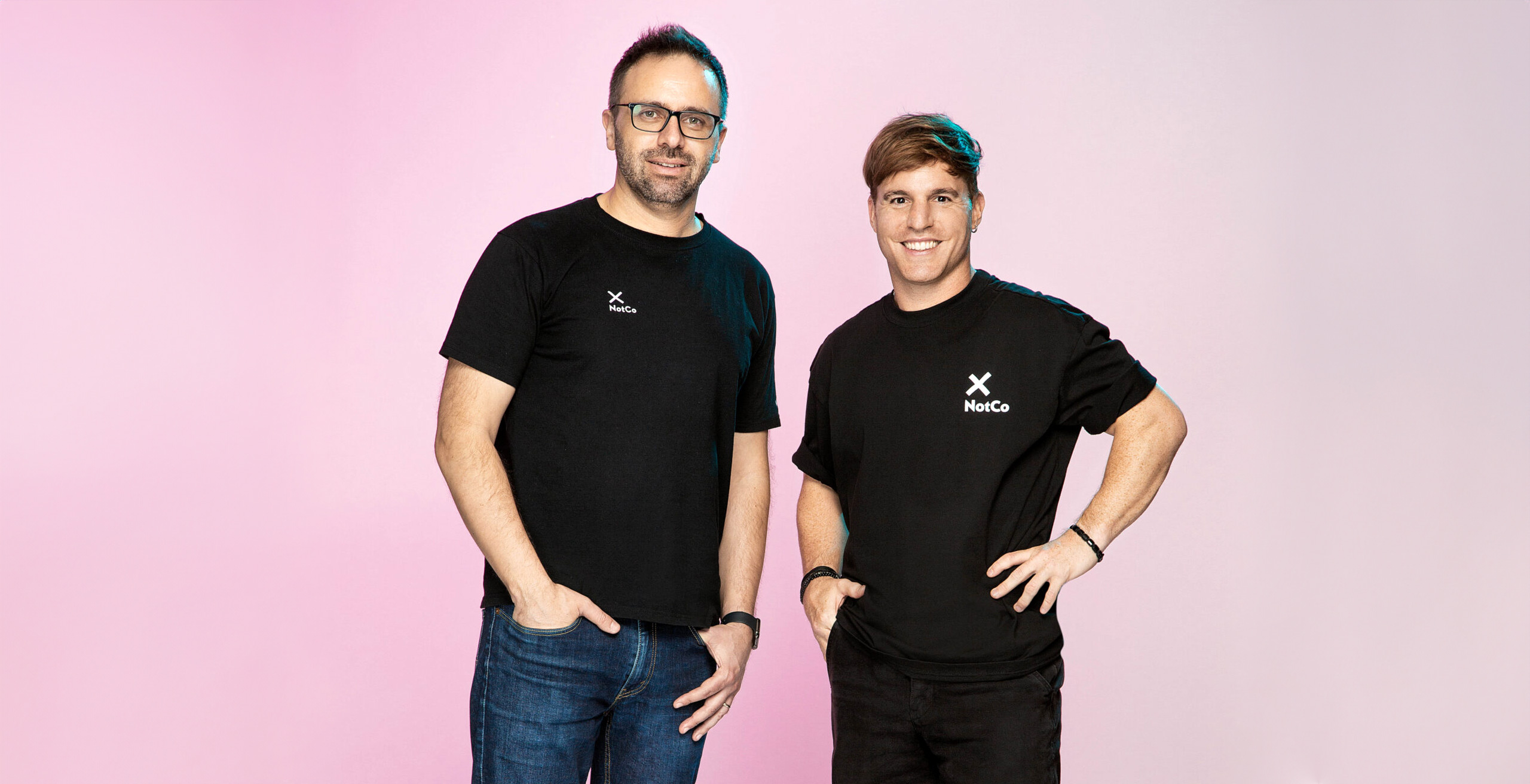
At Berkeley, Matias learned that pharmaceutical R&D relied on AI to discover new medicines and formulations. What if food companies could do the same? To find out, Matias needed an AI expert, which is how he found himself in Karim’s office in 2015. At the time, Karim was applying AI to astronomy, but he quickly decided that changing the food system would be more meaningful.
He and Matias began developing NotCo’s AI, which they dubbed “Giuseppe” in June 2015. They soon discovered that Giuseppe was limited by a lack of data on the plant molecules that govern our experience of food, from smell and taste to texture and appearance.
So, Matias got an introduction to Pablo Zamora, a Chilean biotechnology professor at University of California-Davis who specialized in plant physiology. He referred Matias to Rodrigo Contreras Arredondo, a professor at the University of Santiago with similar credentials. Rodrigo made significant upgrades to Giuseppe. Both eventually joined NotCo—Pablo as a co-founder and Rodrigo as manager of research.
With Giuseppe working better and NotCo ready to test product-market fit, the team pitched The Hershey Company on developing plant-based milk chocolate. They flew to Hershey headquarters in Pennsylvania to present NotChocolate, their first product. Hershey loved it — so much so that they asked NotCo to sign an exclusive partnership. Matias and Karim declined, fearing that an exclusive deal would cap NotCo’s potential.
“IndieBio is the NASA of food”
Matias Muchnik, CEO, NotCo
Throughout 2016, Matias and his PhD co-founders made, packaged, labeled, and delivered their first commercial product, NotMayo, for Chilean supermarkets. Meanwhile, Matias kept an eye on food tech news, which is how he stumbled upon IndieBio, venture firm SOSV’s biotech startup program. IndieBio had invested in two of the biggest names in animal-free foods: UPSIDE Foods (formerly known as Memphis Meats) and The EVERY Company (fka Clara Foods). “I thought, holy shit,” says Matias, “IndieBio is the NASA of food.”
The NotCo team sent over food samples and joined several calls with IndieBio’s crew to review their science and technology. NotCo was accepted.
Matias represented NotCo full-time in San Francisco, while Karim traveled back and forth from Santiago. They mostly remember pitching investors—again and again and again—as they refined NotCo’s story.
That work paid off. Halfway through the program, IndieBio scheduled a trip to meet investors in Argentina. After pitching Hernán Kazah, a co-founder of MercadoLibre (Latin America’s largest tech company), NotCo raised a $3 million seed round led by his venture firm, Kaszek. NotCo graduated IndieBio in September 2017 with a powerful story and the funding to start work on new products.
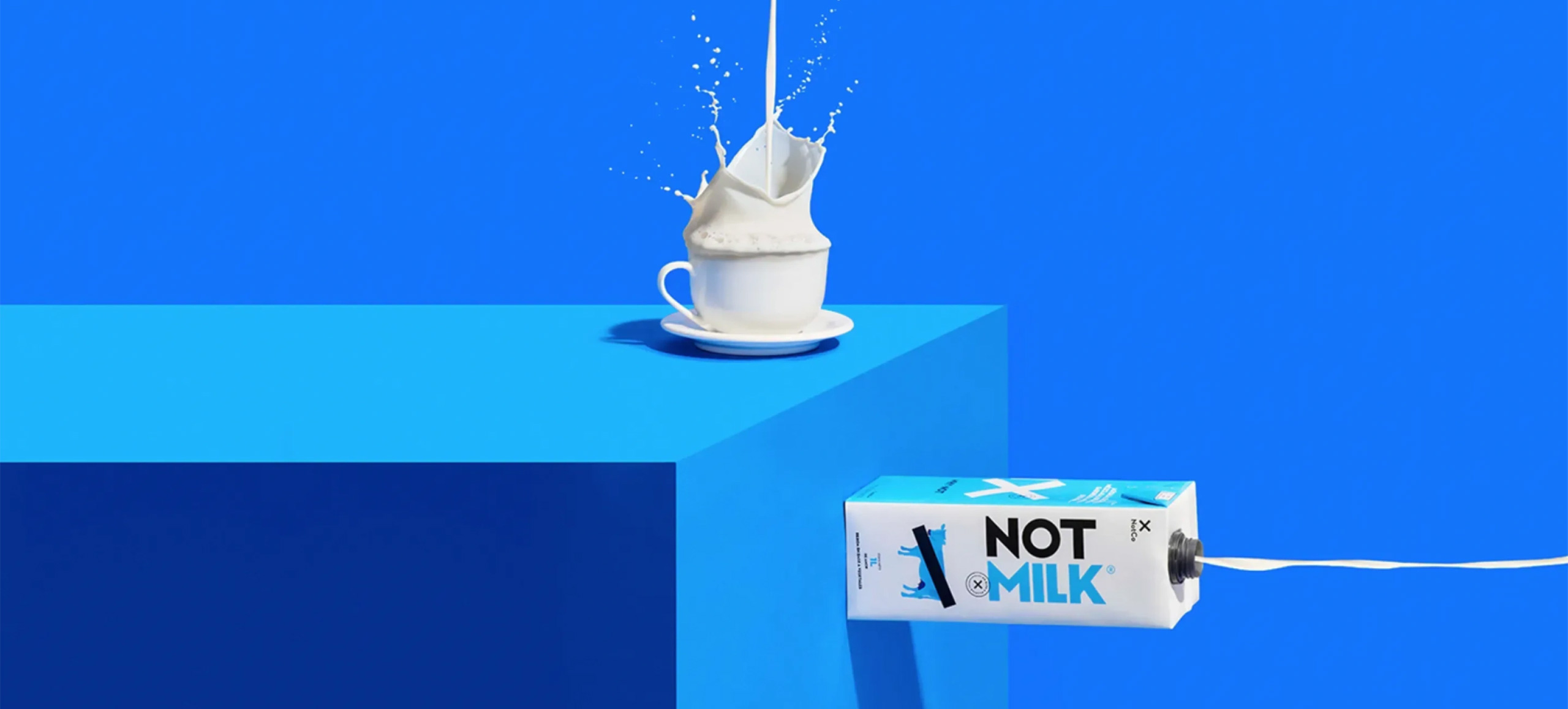
Matias and Karim decided to expand NotCo in Latin America first. That came with a challenging advantage. US and European vegans had learned to tolerate meh-tasting substitutes for meat and dairy. In Latin America, there was almost no vegan culture. NotCo would only grow if it outcompeted animal foods.
Giuseppe made that possible. Giuseppe analyzes food at a molecular level to come up with plant-based recipes that replicate the flavor, texture, and nutritional profile, shortening the R&D process from years to months. Giuseppe draws on a proprietary database of more than 300,000 edible plants, which means it sometimes produces surprising formulations—like using pineapple and cabbage juices to make NotMilk taste like milk.
Matias and Karim believe that Giuseppe will become the R&D intelligence inside major food brands. That’s Giuseppe’s role in the Kraft Heinz Not Company joint venture created to come up with plant-based versions of Kraft’s classic products. Giuseppe can also help food scientists rapidly reformulate existing products if, for instance, supply chain issues, disease, or climate change lead to ingredient shortages. Today, Giuseppe’s outputs have led to more than twenty-four international patents.
Potentially, Giuseppe could disrupt R&D in any industry that relies on complex recipes, including supplements, pet care, and beauty products. That’s why Matias calls NotCo a Trojan horse—it’s a data company disguised as a food company. And it’s now behind the ramparts, positioned to replace animal ingredients in numerous industries. That’s welcome news for our warming planet.
By Richard Ellis
Photos by NotCo